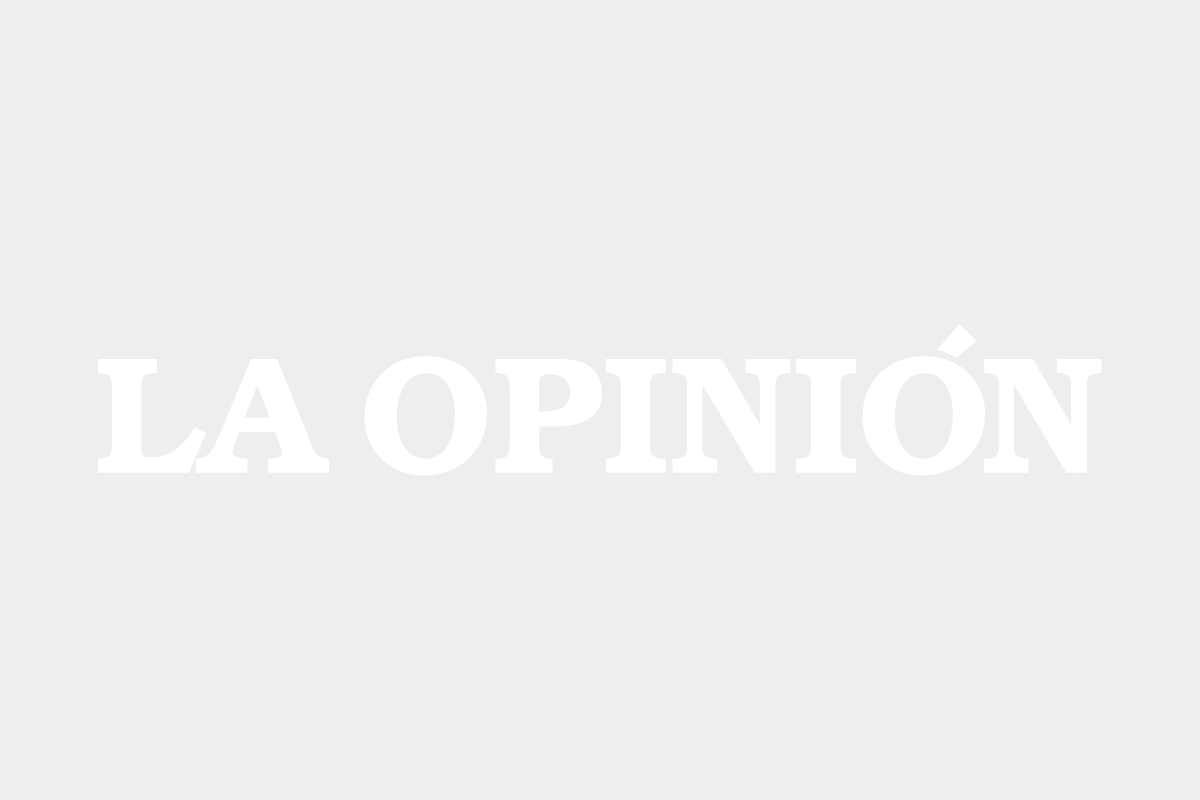
Por REDACCION
Por Diego Yañez Martínez (La Nación), 4. - Siempre supo lo que quería. Cada vez que sentía el ruido inconfundible de un motor al encenderse, cada vez que lo vencía la curiosidad y se adentraba en entender su funcionamiento, o simplemente fijaba su vista por unos segundos en un modelo que le despertaba su admiración, como si nada más existiese, ratificaba su convicción: debía perfeccionarse y estudiar ingeniera automotriz. Era el primer paso; al destino que hay que ayudarlo.
El resumen de Witold Kopytynski diría lo que sigue: fue anotado en el registro civil hace 30 años con el mismo nombre que su padre. Argentino de ascendencia polaca, estudió ingeniería industrial en la UCA y se recibió en tiempo casi récord. Con sus ahorros se costeó la maestría en el Technische Hochschule Ingolstadt, una prestigiosa universidad alemana apoyada por Audi, donde al poco tiempo empezó a trabajar.
Su tesis, basada en sensores que detectan que al abrirse la puerta de un auto no choque con nada, fue patentada por su empleador. Se graduó y creó su propia empresa que, a poco más de un año de sus inicios, ya cuenta con 11 empleados, además de los cuatro fundadores, y busca revolucionar a la industria automotriz cambiando el modelo de producción.
ARCULUS
Los orígenes de Arculus, como decidieron llamar a la compañía con los otros tres socios, son recientes y se remontan a tan sólo un año atrás. La inversión inicial provino del propio gobierno alemán. El proyecto ganó una beca de 150 mil euros (el dinero no se devuelve) a través del programa de financiación Exist, del Ministerio de Economía y Energía, enfocado en startups y tecnología, y otra de 36 mil euros. Además recibieron 25 mil euros de un programa acelerador de incubadoras. En menos de ocho meses ya obtenían ganancias.
SISTEMA
MODULAR
El sistema modular que desarrollan, según aseguran, puede ser hasta un 30% más eficiente que el actual. Se separan todas las estaciones de la línea de producción, y se colocan en un área 2D de cualquier dimensión y forma, cada una ocupando un cuadrante (una estación de seis metros por seis metros). Todos los productos son transportados sobre robots autónomos de un módulo independiente a otro, eligiendo siempre el óptimo para minimizar tiempos.
"Esta idea surge como solución a complejos de producción en la industria automotriz. Hace 100 años Henry Ford decía 'el cliente puede comprar cualquier color, siempre y cuando sea negro'. Hoy, todos los autos son diferentes. La cantidad posible de variantes, por ejemplo, del modelo A3 de Audi es de 40 cifras. No todos los productos necesitan los mismos procesos, ni los mismos tiempos y todavía se siguen produciendo en este sistema que fue diseñado para productos estándar", explica Kopytynski a La Nación por Skype, desde Alemania.
Para apoyar su postura recita de memoria algunos ejemplos y señala por caso que todo el sistema se frena hoy si hay un problema en la línea de producción y el costo de un minuto de inactividad es de 25 mil euros en Alemania, o que el año pasado Volkswagen perdió más de 400 millones de euros por cerrar una línea de montaje por una semana.
"Se dice que estamos en la cuarta Revolución Industrial con todos los avances que produce la tecnología. La nueva era es de customización masiva. BMW declaró que el año pasado no hubo dos autos de los que hayan producido que fueran iguales", agrega.
La empresa ya tiene varios proyectos aprobados por Audi en marcha. En noviembre del año pasado, ante 150 periodistas que cubrían el TechDay Smart Factory de la automotriz alemana, se hizo una primera demostración y tuvo mucha repercusión. "Pequeñas estaciones de trabajo separadas permiten rutinas altamente flexibles en términos de tiempo y espacio. Así, entre estos puestos, los sistemas de transporte sin conductor, controlados por precisión con un ordenador central, asumen el traslado de las carrocerías de los autos, así como las piezas necesarias para la producción reduciendo costos de logística", explicaron.
Kopytynski vuelve sobre los propios números de la compañía de los cuatro aros para enumerar las ventajas que implica la producción modular. "Cada 88 segundos sale un auto de la línea. Pero hay algunos que necesitan 60 segundos y otros 130 para terminar un proceso. En nuestro sistema, todos los módulos son independientes, y cada uno puede tomarse un tiempo diferente para terminar el proceso sin afectar a los demás", apunta.
Las pruebas del nuevo montaje se están desarrollando en la planta de motores que Audi tiene en Gygor, en Hungría, y su aplicación está prevista en tres proyectos más antes de fin de año. Además Arculus está negociando para conseguir el proyecto del nuevo modelo Urus de Lamborghini y busca implementar el sistema en las fábricas de Volkswagen y Porsche.
Los comentarios de este artículo se encuentran deshabilitados.